Future Innovations in Dental CAD/CAM Technology
Future Innovations in Dental CAD/CAM Technology
Blog Article
The globe of dentistry has experienced a cutting edge improvement over the last couple of decades, with dental CAD/CAM (computer-aided design/computer-aided production) technology at the leading edge of this advancement. This modern advancement uses sophisticated software application and specific machinery to design and manufacture dental repairs, such as crowns, bridges, inlays, onlays, and veneers. Dental CAD/CAM milling burs are a crucial part in this procedure, playing a crucial role in forming complex dental remediations with amazing accuracy.
Milling burs are cutting tools made use of together with dental milling makers to sculpt out and complete dental prosthetics from various products. These devices should be sharp and extremely sturdy, offered the accuracy required and the hardness of products they commonly deal with. Typical materials include ceramics, materials, and metals, although increasingly, zirconia has come to be the material of selection for numerous dental restorations because of its superior stamina, biocompatibility, and visual potential.
Dental zirconia spaces, occasionally referred to as zirconia discs or blocks, are pre-manufactured forms of zirconia utilized in the milling procedure. Zirconia, a crystalline kind of zirconium dioxide (ZrO2), stands apart for its mechanical properties, which approach those of metals. These homes include high fracture strength, resistance to wear, and a color that closely mimics all-natural teeth, making it excellent for dental applications. The manufacturing of dental zirconia starts with the formation of these blanks. They are fabricated under high stress and temperature level conditions, which impart premium thickness and mechanical qualities.
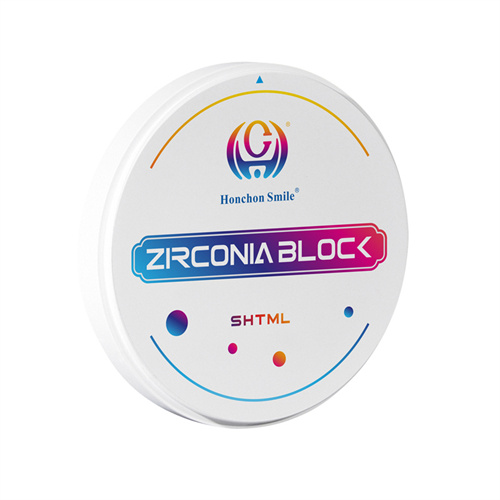
Explore the most recent innovations in dental CAD/CAM innovation, zirconia milling, and 5-axis dental milling devices that are revolutionizing corrective dental care. Discover how technologies like Dental Zirconia blank are enhancing precision, person, and effectiveness complete satisfaction in modern-day dental treatment.
When the zirconia blanks are created, they require to be sintered, usually in a zirconia sintering furnace. Sintering is a thermal process created to produce a strong mass from powder without melting it. During sintering, the zirconia bits fuse together at high temperature levels, enhancing the product's density and mechanical homes while achieving the preferred translucency and color gradients. A zirconia sintering furnace is a customized piece of tools efficient in acquiring the high temperatures needed for this process, usually in the variety of 1350 ° C to 1600 ° C. The sintering process is important, as it stabilizes the zirconia framework and locks in its biocompatible and visual top qualities.
Advanced milling makers, particularly 5-axis dental milling devices, have actually changed the production of dental remediations. Generally, dental reconstructions needed labor-intensive procedures and a considerable amount of time to create. This gives the milling machine the flexibility to approach the zirconia blank from any type of angle, which is critically crucial for developing intricate shapes and damages properly and successfully.
These ingenious materials combine the benefits of multi-layered zirconia with the precision of 3D printing technology. The multi-layered facet refers to the slope in shade and clarity within the zirconia block, imitating the natural transition from dentin to enamel found in actual teeth.
3D printing modern technology has actually included one more layer of customization and precision to this approach. By incorporating CAD/CAM layouts with 3D printing, the complex details of the dental remediation can be captured and published layer by layer. This brings about also higher accuracy in fit and aesthetic appeals, which is critical for client complete satisfaction.
The combination of dental CAD/CAM systems, premium milling burs, dental zirconia blanks, cutting-edge sintering furnaces, 5-axis milling equipments, and the most up to date advancement in 3D plus Multilayer Blocks exemplifies the future of dental prosthetics. These innovations not only ensure accuracy and dependability however also streamline the production procedure, making it quicker and more cost-effective. The causal sequence of these innovations extends much beyond laboratories and manufacturers. Dental professionals can offer better solution with quicker turn-around times, while clients gain from even more long lasting, better-fitting, and aesthetically pleasing restorations. The change from standard methods to electronic process in dental methods highlights the move in the direction of enhancing accuracy, performance, and total client experience.
The accuracy managed by these innovations means prosthetics can be developed and made with a high degree of accuracy, decreasing the need for repeated installations or modifications. This degree of precision is mostly driven by the high quality of dental CAD/CAM systems and using exceptional milling burs capable of great outlining. Furthermore, the handling of dental zirconia spaces in zirconia sintering furnaces makes certain that the end product satisfies the highest requirements of longevity and biocompatibility.
The introduction of 5-axis dental milling makers has actually widened the range of what is feasible in corrective dentistry. These makers can mill facility geometries and fine information which were not possible prior to, leading the method for extra advanced dental remedies. This technical leap has additionally made it feasible to leverage 3D plus Multilayer Blocks efficiently. These multilayer blocks give natural-looking restorations that replicate the rank of shade and clarity found in actual teeth.
Additionally, the continual development in zirconia materials and CAD/CAM modern technologies continues an extra efficient and effective dental treatment atmosphere. Dentists can now attain even more predictable end results, minimizing chair time and improving patient fulfillment. The comprehensive combination of these innovations right into routine dental method symbolizes a seismic change from responsive to positive dental treatment, where digital impacts, accurate milling, and instant adjustments come to be typical practice.
Another crucial facet is the financial and environmental benefits these innovations bring. By minimizing product waste and enhancing using resources, dental techniques can run more sustainably. The efficiency gains also convert right into cost savings that can be passed on to clients, making high-quality dental care more accessible. The global combination of these innovative products and makers right into dental educational program guarantees that future dental experts are skilled in the most recent technical developments, promoting a culture of continuous enhancement and innovation.
In summary, the harmony in between dental CAD/CAM systems, durable milling burs, top quality zirconia spaces, reliable zirconia sintering heaters, modern 5-axis dental milling equipments, and revolutionary 3D plus Multilayer Blocks is driving a brand-new age in dentistry. This mix is transforming how dental remediations are designed, fabricated, and applied, resulting in much better results for both individuals and dentists. As technology remains to evolve, the future holds much more assurance for innovations that will further transform dental care, making it more accurate, effective, and patient-friendly than ever in the past. Report this page